Hayes Original Jaw Couplings
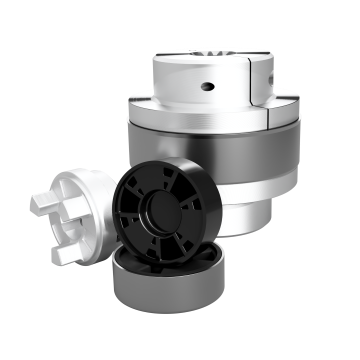
Hayes Original Jaw Couplings
When the L-Series Jaw Coupling just isn’t getting it done. Install our Hayes Jaw Coupling and watch your problems dissolve away. For most OEM’s, jaw coupling failures are costly and time consuming.
We make these jaw couplings from both steel and cast aluminum. These jaw couplings are precisionly machined to ensure a perfect fit and perfect alignment in your application. You can choose between neoprene rubber inserts, or Hytrel inserts. When selecting the neoprene insert we suggest the use of a metal ring to help protect over flex in the inserts.
If you have a tough application that is running submerged, or is just in a harsh/wet environment we suggest the use our our Hytrel insert. We keep many sizes in stock and have plenty of room in our driveway for those times you need to send a helicopter for a coupling emergency (yes, this really happens sometimes) .
This simple, three piece, quality built, flexible jaw coupling is generally used to connect an electric motor to a hydraulic pump or mechanical drive. The hubs are made of a strong, lightweight aluminum alloy.
The bodies and lugs are precision machined on CNC equipment to assure proper fit every time. Two set screws are standard. The solid wall of rubber in the insert eliminates metal-to-metal contact and provides a clean, quiet, trouble-free performance when aligned properly.
The unique steel locking insert is standard on all splined couplings in the 20 through 60 series. For the mobile market, taper lock splines are also available in the same series. Three insert choices are available. Neoprene, Hytrel* and Neoprene with a metal ring.
Neoprene is used for light or steady loads. Hytrel*, for industrial application where torque, a variety of load conditions or chemicals exist. Neoprene with a metal ring for medium and heavy torque conditions and internal combustion engine applications. Installation of these jaw couplings requires only a straight edge and feeler gauge to ensure proper alignment. For longer insert life, misalignment should not exceed .005 parallel or 1° angular
L-Series Jaw Couplings
You’ve seen them all over on shaft-to-shaft applications – maybe even in your local hardware store. The addition of our L-Series Jaw Coupling line has proven that you can rely on Hayes for all your couplings needs. Replacing existing couplings (of similar design) with the Hayes L-Series may save you some $$. We manufacture a full range of the L-Series Jaw Coupling (L035-L225), with both English and Metric bore options.
Our L-Series jaw coupling is offered in a large variety of bore and key options, as well as splines. These jaw couplings are designed for a range of different applications using electrical motors as well as internal combustion engines. This design offers a standard shaft-to-shaft connection ideal for many industrial duty applications. In addition, you can interchange this jaw coupling with other popular domestic brands.
The addition of this product to our extensive list of power transmission products allows us to provide our customers with a diverse, and economical product line. Couplings are sintered iron and available with a number of different drive elements: Buna-N, Urethane, and Hytrel
Curved Jaw Couplings
You’ve seen them all over on shaft-to-shaft applications – maybe even in your local hardware store. The addition of our Curved Jaw Coupling line has proven that you can rely on Hayes for all your couplings needs. Replacing existing couplings (of similar design) with the Hayes Curved Jaw Coupling may save you some $$
This three-piece curved jaw coupling design was specifically designed to reduce the edge pressure of the driving lugs to the insert. These jaw couplings are perfectly interchangeable with other German and Italian designs of the same type. Hubs are made in both aluminum, and steel.
The elements, or spiders, are made from variable durometer urethane. Available in 10 sizes, bores to 110mm (4.33). These couplings are great for electric motor driven pumps, gearboxes, conveyors, as well as applications with reversing loads, due to compression nature of the design. These jaw couplings are torsionally flexible and designed to dampen operational vibrations and shock loading.
With the teeth of the spider being crowed, to avoid edge pressure, it allows for greater shaft misalignment’s over couplings of a similar design (Straight Jaw). With the concave tooth design this coupling is subject to a pressure only load as compared to other straight jaw couplings, which are prone to a bending stress as well. Due to this difference in driving ability, the jaw coupling will withstand considerably higher loads.